Make-up for Metal(金属のメイクアップ)。そう掲げるのは、戦後間もない1947年に設立した電化皮膜工業(東京都大田区、秋本恭一社長)。モノづくりの集積地である大田区で同社は一貫してアルミ表面処理やめっき化工を行っている。前編では同社の強みやIT化の取り組み、材料価格の高騰・新型コロナの影響について、後編では人材育成について廣門伸治専務に聞いた。
ー簡単な会社・事業概要の紹介をお願いします。
東京・大田区で一貫して表面処理を行っている会社で、設立は1947年で76年目になる。主にアルミニウムの表面処理(アルマイト)や硬質クロムめっき処理などを行っている。金属に様々な表面処理を施すことで、その特性をさらに高めることや、新たな機能を付加することができる。取引先業種としては、半導体製造装置や航空・宇宙・防衛、ロボットなどの産業機器である。当社の特徴として、量産ではなく一品一様で処理していくことが多く、月に約400社、年間で700-800社ほどのお客様と取引をしている。2009年に航空・宇宙産業の品質マネジメントの国際規格「JIS Q 9100」を取得し、品質を担保するための様々な分析装置を取り揃えている。先進の技術を持つ東京地区の航空宇宙部品製造企業連合「アマテラス」や大田区の町工場から世界を目指す「下町ボブスレー」にも参画している。
昔は大田区周辺でも量産生産を行う会社もあったが、本社機能や工場が地方、海外に移っている。実際に大田区内の事業所数も減少の一途をたどっている。当社も昭和の時代は自動機のラインがあり量産をしていたが、時代の流れとは逆行して、平成に入ると小ロット・個別生産にシフトをして、現在に至る。
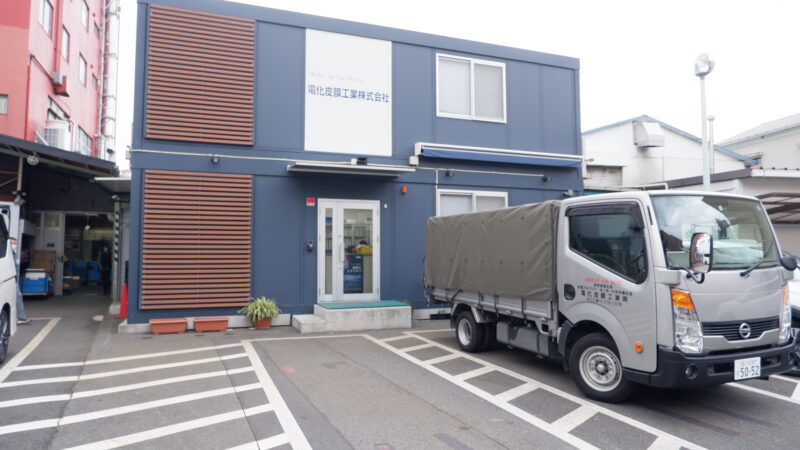
ー昨今の新型コロナの影響や材料費の高騰などの足元の影響は?
新型コロナの影響では、航空産業の落ち込みに比例して、当社も影響を受けた。一方で半導体関連が活況で、その落ち込みを埋めてくれた。2019年の売上を100%としたら、2020年は20%落ち込み、21年で10%戻し、22年は21年と同水準というイメージだ。
材料費の高騰に関しては、当社で取り扱う薬品は2022年に入ってから約2割は値上げしている。5,60種類の薬品を取り扱うが全て値上げしている。電気・ガス料金も値上げしているのも悩みの種だ。
ーその中で価格の転嫁などはできていますか?
薬品の値上げ分に関しては、昨年の6月くらいからお客様にお願いをし始めた。一律ということではなく、個別に依頼している。当社の多くのお客様は、(最終メーカーではなく)金属加工業者などが多く、その会社もその上のお客様への価格転嫁が出来ない場合は、難しいといった場合もある。事情を分かっているお客様には、価格転嫁を了承してもらっている。
一方で原価を抑えるという意味合いでも、今まで以上に「失敗をしない」ということが重要だ。この10年くらいでIT化を進めていて、見積書や作業指示書、技術情報など担当者ごとに保有していた情報は社内でオープン化している。そのため、コロナ禍で担当者が出社できない時でも、大きな支障がなく、進められたことは大きかった。
ー具体的にIT化とは?
ITシステムは2012年からアプストウェブ(東京都千代田区)が開発する「コンテキサー」というシステムを導入している。見積情報の管理や発注指示書の管理・発行だけでなく、工程進捗も確認できる。工程進捗については、指示書にあるバーコードを各工程が終わるとスキャンすることで、今どの工程の段階かが分かる仕組みだ。そのため、お客様からの納期の問い合わせに対して、現場に確認しなくても、営業担当者がコンテキサー上で工程情報を確認して回答することができている。納期管理も一覧表で確認できるため、効率の良い作業ができ、無駄な残業も減っている。製品ごとのクセや特記事項もデータとして保存できるため、作業自体の効率化、不良率の減少にも繋がっている。
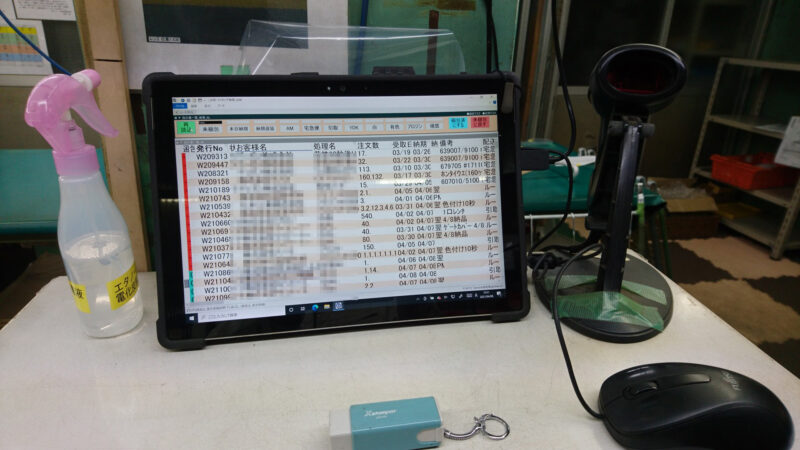
ーIT化を進める中での苦労や今後の展開は?
現在、取り組んでいるのが技術情報のデジタル化だ。「Aという製品は、このようにセットした方が失敗しない」など、製品個別の化工の仕方がある。今まではそういった技術情報はノートに書いていたり、担当者の「頭の中」に入っていた。毎月行っている作業であれば、記憶を辿ってできるかもしれないが、半年など経つと忘れてしまう。そうなるとノートのその部分を探すのにも時間が掛かり、担当者が代わった場合は、その情報が継承出来ないかもしれない。
そういったこともあり、図番や品番を登録して、データ検索すれば図面や化工方法などの特記事項などをすぐに閲覧できるような状態にするのがベストだと思っている。「記憶」ではなく「記録」を見ながらやっていきましょうということだ。
2018年くらいから、この取り組みを始めているが、当初はなかなか進まなかった。理由は周りに人がいることが当たり前だったからだ。作業が分からなくても、現場で教えてくれる人がいれば、困らない。誰かが休むということは皆、想定していなかったし、例え休んだとしても、突発的な問題との認識だった。そのような状況が変わったのが、2022年春。家庭の事情で休まなければいけない社員がいて、その人が行っていた作業をデータ化する必要性がでてきた。必要に駆られたことで社員も重要性を認識し、現在は約600件の情報がデータ化された。
ー担当者が自身でデータを取り込むのですか?
作業中は手袋をしているため、それを自身で取り込んで編集するのは、少し無理があると考える。現場で撮った写真を私が整理・データベース化をしている。当初は、デジタルカメラで撮影してもらっていたが、後からデータを取り込むため編集は難しい。現在は、運用効率を上げるために自分のスマートフォンで撮影してもらい、転送してもらっている。図面と全体写真とフォーカスした写真の三点を撮影して図番などを入力してデータベース化し、検索がしやすいようにしている。この取り組みはさらに推進していく。
ーーーーー
インタビューの後編「【中小企業インタビュー】世代間の技能伝承はすでに取り組み済。次のステップはスペシャリストの育成へ。電化皮膜工業 廣門専務(後編)」は明日公開予定です。
ーーーーー